iam replacing current bearing and have new ones although have hammered away the old corroded bearing balls etc but cant seem to get the last little silver ring thing out which is closest to the edge.
Please view pics!!
Please view pics!!
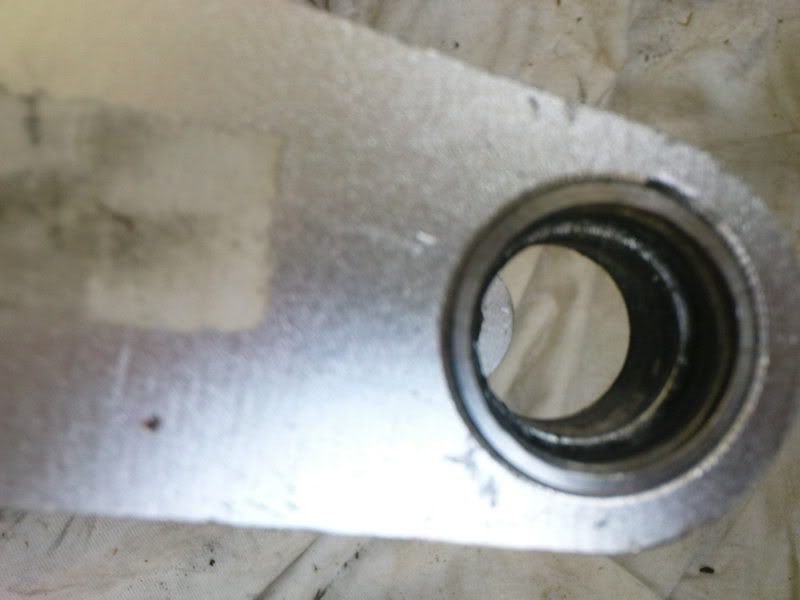
Have the same problem, cant get mine out tried with a screw driver and hammer dosent come out arggghh!
Where abouts r you located?Have the same problem, cant get mine out tried with a screw driver and hammer dosent come out arggghh!
have you got a socket that will fit in there and grab the sleve?
hitting it with even force on all edges is the key to getting it out
Where abouts r you located?
To far from me.... You could just purchase one of these, they come in handy for quite a few things.Dandenong 3175, Melbourne
I like that ideaif you have a long bolt or piece of threaded rod about 300mm-500mm long.
(Bunnings sell a 10mm threaded rod approx 500mm long for about $6)
you can slip that inside the bearing/bush from them outside of the swing arm, and put a couple of thick washers and nuts on the inside end of the thread.
p.s. make sure the washer can fit inside the swingarm.
then on the outside section of the swingarm, slide an old hammer head or 3lb mallet head over the thread, then add a couple of thick, large o/d washers and a couple of nuts to stop the hammer head comming off the end of the thread.
you now have a makeshift slide hammer,
slide the hammer head down towards the swingarm, then hold the hammerhead, and quickly slide it to the washers/nut end near you, at the end it will hit on the washers and stop.....
watch you don't pinch your fingers when it hits the end.
a few hard whacks with the hammer head should pop the bearing/bush out.
Enter your email address to join: